When comparing different alternatives for automated warehouses, it’s vital to examine the financial impact with a wider perspective to see and understand the real benefits and limitations different alternatives can offer, and how these affect the connecting processes. A properly-done TCO- analysis provides a broader view, not only to clarify the investment goals, but also to compare different alternatives.
Why an automated warehouse?
In the past, the need for warehouse automation in paper mills was mainly related to operational volumes. When stacking rolls on the warehouse floor using forklifts got too hectic, overhead cranes were taken in use. This improved the warehouse’s density and safety. By eliminating forklift traffic in the warehouse, the driving aisles are also eliminated, and the available space for actual product storing could be fully utilized. Forklift aisles, needed to manage the inventory, easily take up 50% of the floor space in practice. Also, the roll stacks’ heights could be doubled with cranes from 5x to 10x of the roll diameter, which also increases the storing density per m2 by raising the warehouse roof from 12 meters up to 23 meters.
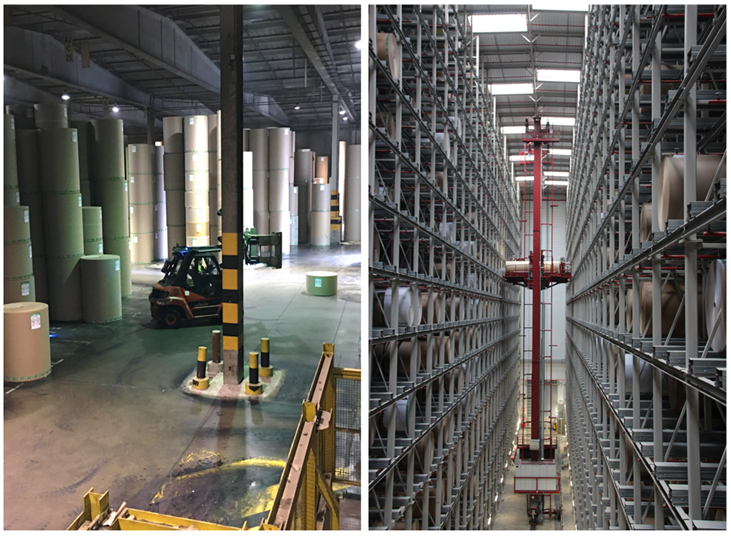
New era – new requirements
Today, the reasons for warehouse automation have shifted from the need to cope with bigger volumes to better control of the inventory as part of the supply chain. Reasons for this development is the well-known industry’s structural changes due to the digitalization combined with raised sustainability demands. These megatrends have changed the direction and mindset in the paper industry, as it has done almost in every other business too. There is more information available for all, and there are more alternatives to choose from.
To compete as a producer in this environment, automation is a must to be able to respond to customers’ preferences efficiently. Suppliers need to be able to manage the whole supply chain from raw materials to order fulfillment better than their competitors to survive and serve with required accuracy, speed, and quality. Warehouse automation is cutting what used to be two weeks’ lead times down to two days, with 100% accuracy and 0% broke. In distributed manual warehousing, rolls could be handled as many as 12 times before dispatching them to the customer. In centralized automated warehouses roll handling is reduced to only one movement in and one out to dispatch.
Accelerating change
Today, 30% of Europe’s paper mills with over 200,000 metric tons annual production have automated their warehouses for finished or intermediate products. When the bar is raised to mills with over 500,000 metric tons annual production, half of the mills have automated their warehouses. This is the result of thinking that only big volumes need automation. In North America, the levels of warehouse automation are to catch up with those of the European counterparts. But the reasons for automation are now changing due the megatrends explained above, which are accelerating the change towards automation. It’s not about volume management anymore, it’s about how to deliver products faster, with more flexibility, and ultimately cutting costs across the whole supply chain. In other words: how to change the reactive supply chain to be proactive, how to be able to react faster to changes in the market and customer demands.
Key features to be compared
A supply chain model means how mills are producing and distributing specific products to their customers. Common practice used to rely solely on reactive “Make to Order” (MTO) model, where manufacturing is driven by orders. But if you want to excel with speedy deliveries, beat your competitors by weeks with reduced lead times from order to delivery, you also need to be able to manage the “Made-to-Stock” (MTS) model from a single warehouse, not from a distributed network of warehouses. This defines the key features that automated warehouse needs today, and why manual work in warehouses is disappearing. It’s about the density to be able to store needed volumes (tons) in one warehouse within available space at the mill, as well as handling capabilities to able to manage the mixed content to ensure short turnaround times for transportation logistics.
See the summary of main characteristics of different warehouse types used in paper mills and converting plants:

HBW deep = High-Bay Warehouse, rack type ASRS to store rolls on deep storing channels
HBW single = High-Bay Warehouse, rack type ASRS to store rolls on single roll channel pocket
OHC = Over-Head Crane ASRS to stack rolls on floor
AGV = Automated Guided Vehicle, rolls stacked on floor
Manual PIT = Manually operated Powered Industrial Trucks equipped with clamps to stack rolls on floor
The differences between handling and sorting capabilities are explained by how rolls are handled through the warehouse. Deep channel high-bay warehouses are handling the rolls in sets, compared to other alternatives which handle single roll or pair of rolls at once. When you handle 2-6 roll sets per cycle, instead of one roll, you have 2-6 times bigger handling capacities per equipment. This also lowers the overall need of equipment in the system accordingly.
And the big difference in storing density is explained partly with the maximum roof heights different concepts allow. Flexible high-bay rack storages can be anything between 10 and 40 meters, when overhead crane storage heights are limited to 25 meters and AGV and manual PIT warehouse to 10 meters.
The above-mentioned handling capacity affects to the storing density too. When you have enough handling capacity to reorganize your inventory, you can store also mixed sets. This reflects directly to the practical fill rates different solutions can manage. The fill rate in HBW deep channels is 85%, with overhead cranes it is 70% and with AGV and manual PITs 50% due to the driving aisles.
Total cost of ownership defines the most cost-efficient alternative for both, big and small volumes
Selection of the right warehouse type depends on many issues which vary case by case. These are preferred supply chain model, produced grades, location, surrounding infra and so on. There is no “one-size-fits-all” solution available. But what is clear, is that the most important fact in the selection is the total cost of ownership, comprising both the capital and operational expenses. Also costs, which are difficult to measure, such as improved safety with zero-accident-zones and competitiveness achieved against the competitors with more resilient and agile warehouse operations make a difference.